What we did...
Working with CORRIM (certified environmental consultants) and the University of Washington School of Environmental and Forest Science, we completed what is called a Life Cycle Assessment (LCA) for our planned pilot biochar plant. This analysis estimates how much carbon, after deducting all our operational emissions from ‘forest to farm’, our pilot biochar plant will sequester.
5 key takeaways...
#1 Cradle to Grave
We applied the ICROA-certified Puro.earth standard for biochar carbon removal because we wanted a fully-inclusive impact assessment.

The analysis starts in the forest. It includes emissions from loading small-diameter logs onto log trucks and transporting them to our pilot plant, on a round-trip basis. It excludes harvest related emissions – cutting trees and bringing them to a landing – because those emissions would happen in the de-facto scenario where the small-diameter trees are piled and burned or left to decompose.
The analysis then moves to the plant, where most of the process emissions occur as we convert logs to biochar and its co-products. It includes direct equipment related emissions and also an estimate of the carbon footprint related to the manufacture, maintenance and disposal of the equipment we will be using at the plant.
The analysis then moves to the farm. It includes transportation to the Columbia Basin, integration of biochar into commercial compost and finally transportation and application of the finished compost/biochar mix to fields. Once in the ground, we estimate how long the carbon will be retained in the biochar based on soil temperature and the biochar properties.
#2 Operations are Net Negative
Our process will only emit the equivalent of ~3.4% of the carbon contained in the logs we’ll convert to products. That means we have a huge opportunity to sequester carbon in our products and provide sustainable carbon inputs to other processes (e.g. biofuels).

#3 7,800 Metric Tons per Year
Our pilot plant will sequester over 7,800 metric tons of CO2e per year. And if 7,800 metric tons of CO2 doesn’t mean a lot to you – that is the equivalent of the emissions from 1,700 cars! But that’s just for the pilot, which we’ve intentionally designed on a smaller scale to “de-risk” the business. We’ll cover our scaling plans in a subsequent update.
* EPA avg car emissions = 4.6 metric tons/yr
* LCA estimated 5,900 mt of CO2e revised to 7,800 due to increase of planned pilot capacity
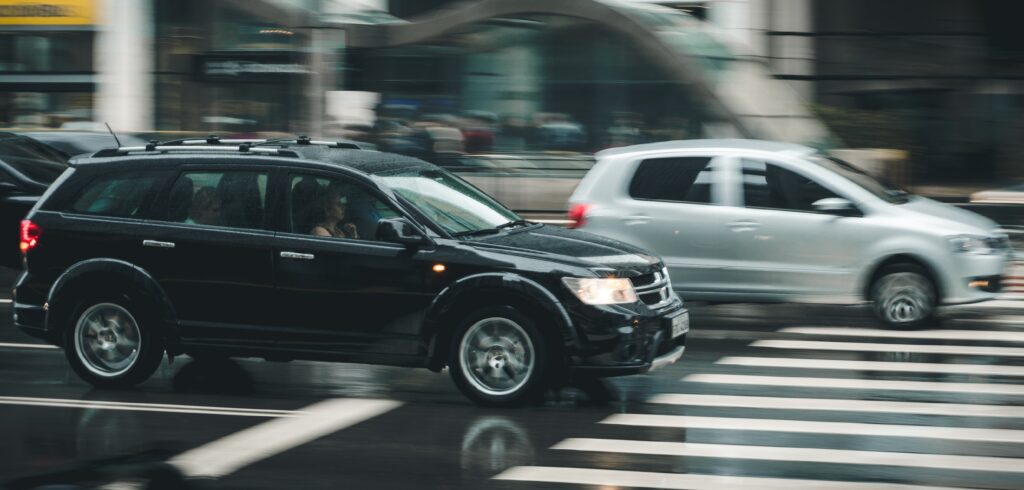
#4 Maximize Electric Operations
In the PNW we are lucky to have access to abundant renewable energy from hydropower and increasingly wind and solar. This is one of the reasons we’ve designed our operation to use as much electrically-powered equipment as possible.
This is challenging for logistics that are still largely diesel-based. Until logistics are more electrified or use more sustainable fuels, the best way to manage those impacts is to locate our pilot plant as close to the biomass and our customer base as possible which is what we’ve done.
We have much more control at the plant. Although diesel-powered equipment is still common for moving biomass around plants like ours, we’re choosing to invest in electrically-powered conveyors for this purpose. This will use less energy that’s more sustainable, and has other co-benefits in terms of safety and operating cost.
In the middle of the plant is a pyrolysis reactor, the machine that converts biomass to biochar. Many reactors rely on propane or other fossil fuel products for heating. We’re considering an electrically-powered reactor which is more sustainable and gives us more control over the process temperatures.
#5 86% of Carbon Sequestered 100 Years Later
Biochar can be a highly durable form of carbon sequestration. Once the carbon from the trees is converted to biochar and applied to the soil, it will remain in the soil for a long time, 100’s to 1000’s of years. Given our projected biochar composition and the soil temperatures in the Columbia Basin region (15 degrees Celsius avg) where we expect it to be applied, the Puro.earth standard projected that 86% of our biochar would still be present in the soil 100 years after application.
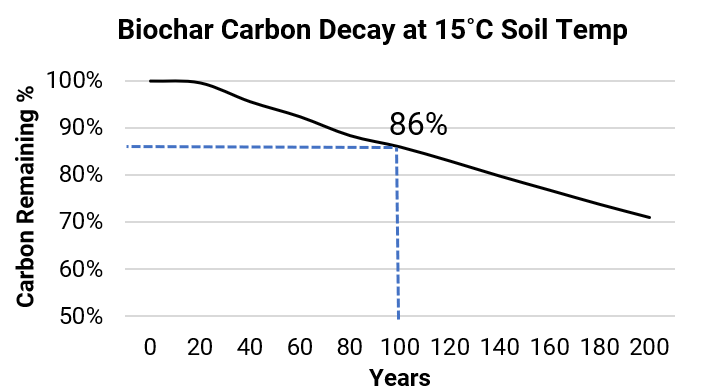
Our Next Steps...
- We’re analyzing the results, looking for ways we can further reduce our emissions.
- We are looking for partners who can make use of the carbon rich bio-liquids that are created as a byproduct of biochar production.
- As we wrap up our equipment selection, we will run another LCA to reflect the new capacity and equipment, likely including scenarios for a couple of different biochar carbon removal standards. Stay tuned for results on that!
Want to learn more?
If you want to get into the details of our Life Cycle Assessment, please find it here.
If you have questions about our Life Cycle Assessment or want to learn more, send us an email [email protected].